Dimensional inspection involves measuring a manufactured part to ensure it meets the specified requirements or tolerances detailed in its design drawings. Tolerance defines the permissible variation from the intended design. This process is crucial for quality control, regulatory compliance, cost reduction, and enhancing manufacturing capabilities. Dimensional inspection is valuable in all stages of manufacturing; including research and development, first article inspection, capability studies, and final inspection.
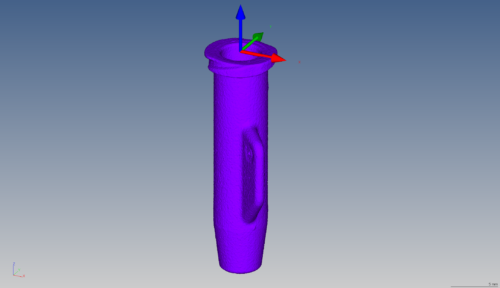
Industrial CT scanning is a critical tool used for the dimensional inspection of medical devices such as Luers and medical connectors, implants, orthopedics, surgical instruments, catheters, stents and drug delivery systems. Some of the common causes of medical device defects are leaky connectors / seals, assembly misalignment, mechanical failures, material fractures, pitting, voids, porosity and variation in material density. By utilizing advanced computed tomography, this non-destructive method captures comprehensive 3D images of both internal and external structures, ensuring that intricate components meet stringent design specifications and regulatory standards.
Over the past decade, DDL has been the leader in medical connector testing. With the introduction of ISO 80369 to address the non-interconnectability and dimensional compliance of various male/female luer components in hospital settings, industrial CT scanning has never been more paramount. DDL has added Industrial CT scanning capabilities to further enhance and complement its ISO 80369 and medical connector testing services in order to serve our clients better.
Whether you have a medical Luer connector, a molded component, a 3D printed component or a CNC machined component, DDL is here to ensure your part is within specification, complies with regulatory requirements and avoids product recalls while keeping patients safe.
Contact Us for more information or to talk to an engineer.