New technologies, process advancements and the aging population have all led to explosive growth within the medical device industry. This growth has also led to more strict and complex regulations with increased competition. The rising regulatory focus and increasing demand for high quality and standard products across the medical device industry has also driven the need for more rigorous testing to ensure a product’s safety and efficacy. To meet this increasing demand for testing, medical device manufacturers face the classic “make or buy” decision of performing testing in-house vs. outsourcing to a third-party lab.
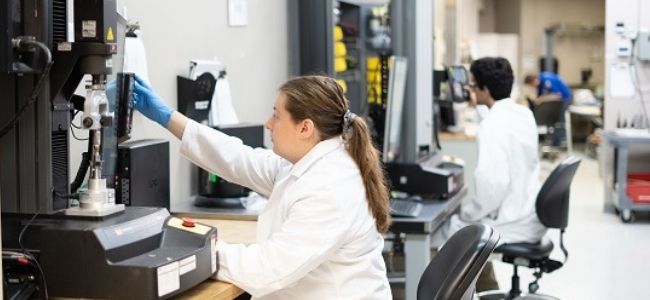
What are the advantages of outsourcing testing?
Cost Efficiencies
The medical device industry is under constant pressure to control costs without sacrificing research development, timelines or safety. Conducting a successful testing program takes significant resources and operational focus. Thus, a medical device OEM must determine if it is more cost-effective to develop this capability in-house, or will it be more efficient to use an outside lab. In most cases, it will be more cost efficient to outsource to a third-party lab.
When doing testing in-house, the largest and most hidden cost is overhead. Medical device manufacturers have to keep in mind the cost to purchase, maintain, repair and calibrate the equipment, building / facility expense, opportunity cost of space utilization, utilities, insurance and any other sunk costs such as administration / accounting expense. Often times, overhead is not accurately accounted for when evaluating the make or buy decision. Companies rely more heavily on variable or operational costs such as CAPEX, labor and direct materials. As a result, the “make or buy” financial analysis can become skewed. By outsourcing testing, medical device manufacturers can take advantage of lowered operation costs, increased agility, a reduction on time-to-market, which can add up to a boost on their return of investment (ROI).
Testing Expertise
In addition to costs, many medical device OEMs may also not have personnel in-house with the appropriate skill set to perform the testing. Testing programs are successful when directed by trained, experienced, and qualified personnel. Subject matter experts play a critical role in assessing product development needs, test requirements, and study designs. An experienced staff brings real benefits from speed of data analysis, operational efficiencies, enhanced reliability, the ability to support data reviews, and numerous other intangibles.
Establishing a robust QMS (Quality Management System) also requires technical expertise. Hiring competent quality personnel to create and maintain standard operating procedures, protocols, and other quality documents is a critical aspect of a quality management system.
If a company seeks to make a long-term investment in device testing, this should also include hiring staff who are experienced in that particular area. This naturally produces cost tradeoffs—the time spent training this new staff will lengthen the time-to-market for any product still in development, and not all manufacturers may be committed to the ongoing recruiting and development of these specialized roles.
Turn-around Time/Reduced Time to Market
Some tests may make sense to have in-house as the difference in turnaround time is minimal. High volume testing can have lengthy turnaround times when conducted in-house compared to outsourcing.
It is also important to determine if the internal lab meet the project timeline based on overall company priorities and resources, which may conflict. This is especially true of larger companies with multiple divisions or product lines that utilize the same laboratory. Every day and every week that testing is delayed also causes delays in getting the product to market, which could ultimately impact cost more to the bottom line than outsourcing the testing to a third-party lab.
Third-party Perspective/Risk Mitigation
When deciding on outsourcing vs. doing a test in-house, one should also take into account the FDA and other regulatory bodies’ perspective on results generated by the medical device manufacturer versus that of a third-party testing provider. While it is generally assumed a medical device manufacturer would not skew the results in order to pass a test, having an outside lab confirm the results of a test always looks better from the standpoint of the regulatory body.
It is also beneficial to have an independent lab involved when performing validation activities in order to have unbiased verification of R&D test results performed in-house. Consider whether regulatory bodies look more favorably upon tests conducted by reliable third parties versus in-house test results based on the criticality of the test endpoint. Using an external third-party laboratory may remove testing bias, or the perception of testing bias, facilitating the path for regulatory approval.
Conclusion
Outsourcing testing offers numerous benefits that can strategically position MDMs for success. Cost efficiency, access to expertise and resources, reduced time to market, and risk mitigation are some of the advantages that make outsourcing an attractive option. By leveraging the capabilities of specialized testing service providers such as DDL, MDMs can optimize their testing efforts, enhance product quality, and improve their bottom line.
For more information, or to answer any testing questions you may have, please contact us or call us at (800) 229-4235.