Following is a discussion with DDL Packaging Engineer, Scott Levy on current trends in package testing and the impact COVID has had on package testing projects.
What is new these days when it comes to package validation testing?
Despite the recent revision to ISO 11607, actual package validation testing itself has not changed too much from the past. The majority of what the updated ISO 11607 standard is talking about is a lot more clarification for the end user. One area that a lot of our client’s overlook is how to execute label inspection as part of the package validation. The FDA lately has been asking quite a bit of questions about adhesion, legibility, etc. from the labels.
How has COVID affected package testing projects?
Tremendously. The first aspect is with customers being able to get specific materials from suppliers for projects such as pouches, trays, lids etc. We have been hearing from many clients that many material vendors are four to six weeks out with various supplies.
Another aspect we are seeing that has delayed package validation testing quite a bit is with backups in sterilization. This alone has had a tremendous impact on how quickly medical device manufacturers can bring products to market, as well as delaying their overall timeline.
These types of delays are dramatically impacting validations as a whole. As a result, projects are taking much more time to be executed. In the past when most customers contacted us to do package validations, they were ready get started right away. Now customers are pushing things out for four or five months, and the overall cycle is much longer.
In working with clients last year during the height of the pandemic, many clients decided they were going to hold tight on their projects and watch their spending. Moving forward into 2021, we are starting to see clients come back because they understand that even though we are still dealing with the pandemic, they need to forge forward with projects.
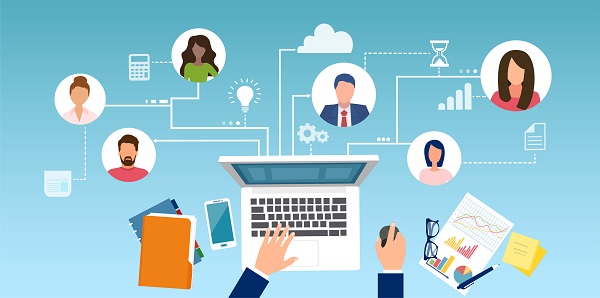
What are some tips that you have for customers doing package testing during COVID?
The biggest tip is when you are working with your supplier is identifying and have all of the information upfront.
With so many people working from home (including many of us at DDL) these days, it has a tremendous impact on throughput with regards to being able to get all of your ducks in a row to be able to speak with your vendors on specifically what you need and the quantities that you need. We understand with engineers working from home they don’t have all this information readily available. However, they need costing quickly so they can go back to the project team and give a projected budget. Working on hypotheticals is exceptionally difficult though for an ISO 17025 laboratory, because we want to have every idiosyncrasy in place so that the project can be put together properly without any issues and everything is 100% documented with the satisfaction and execution of the validation. If cost ends up being the primary reason for moving forward with the project, working on hypotheticals is not a great way to make a decision on which vendor to pick in the first place.
We are also noticing many clients and potential clients who are working from home are often not including a telephone number where they can be reached, so almost all correspondence is happening via teams, zoom or email. Once an inquiry does come through with many questions, many people like to continue communicating via email rather than jumping on the phone. As a result, it can sometimes take up to five or seven email exchanges before the true needs of the customers is fully identified, whereas things could progress much faster with one phone call. For as great as technology is these days, sometimes a simple phone conversation outweighs dozens of back and forth emails to get to the root of the issue.
Do you see any changes coming about with package testing due to COVID?
As was discussed earlier, many companies are moving forward again with projects, as they understand they have to move forward. If the material suppliers and sterilizations start to get back on top of things with better turnaround, package testing will continue to move fast and swift because there’s a lot of projects that did not happen last year that were probably slated to happen. As a result, we are likely going to see an uptick. Thus, why having all the information up front to discuss with your vendor is going to be key and imperative, not only to satisfy your specific requirements right now, but getting the validation together properly to further minimize rework.
Is there anything else you want to add?
At this point, we are all in the same boat. Most of us are working from home and trying to stay safe, as well as keeping our colleagues at the manufacturing facilities, testing labs, etc. as safe as possible. Thus, taking one-step back and having all the information you need up front is key and critical in order to keep things moving forward.